What is Porosity in Welding: Ideal Practices for Staying Clear Of Permeable Welds
Deciphering the Enigma of Porosity in Welding: Tips for Decreasing Flaws and Optimizing Quality
In the intricate world of welding, porosity continues to be a persistent difficulty that can significantly affect the top quality and honesty of welded joints. Recognizing the aspects that add to porosity formation is important in the search of flawless welds. By unwinding the enigma of porosity and carrying out reliable strategies for problem reduction, welders can boost the criteria of their work to attain premium quality outcomes. As we explore the depths of porosity in welding, uncovering the keys to its avoidance and control will be critical for experts looking for to master the art of high-grade weldments.
Comprehending Porosity in Welding
Porosity in welding, a typical problem experienced by welders, refers to the presence of gas pockets or voids in the welded product, which can endanger the integrity and quality of the weld. These gas pockets are generally trapped during the welding procedure as a result of different aspects such as incorrect shielding gas, contaminated base products, or wrong welding specifications. The formation of porosity can deteriorate the weld, making it vulnerable to splitting and rust, ultimately leading to architectural failings.
By recognizing the relevance of maintaining appropriate gas securing, guaranteeing the tidiness of base products, and optimizing welding setups, welders can significantly lower the likelihood of porosity formation. On the whole, a detailed understanding of porosity in welding is essential for welders to produce high-quality and long lasting welds.

Common Reasons For Porosity
When evaluating welding processes for possible quality problems, recognizing the common sources of porosity is important for keeping weld integrity and stopping structural failings. Porosity, identified by the visibility of dental caries or spaces in the weld metal, can significantly compromise the mechanical residential properties of a bonded joint. One usual source of porosity is incorrect protecting gas protection. Insufficient protecting gas circulation prices or incorrect gas blends can result in atmospheric contamination, causing porosity development.
Additionally, welding at improper specifications, such as exceedingly high traveling rates or currents, can produce too much turbulence in the weld pool, capturing gases and causing porosity. By addressing these typical reasons with correct gas shielding, product prep work, and adherence to optimum welding specifications, welders can minimize porosity and improve the quality of their welds.
Methods for Porosity Avoidance
Carrying out effective preventive steps is essential in decreasing the occurrence of porosity in welding processes. One method for porosity prevention is guaranteeing correct cleaning of the base metal before welding. Impurities such as oil, grease, corrosion, and paint can lead to porosity, so detailed cleaning making use of suitable solvents or mechanical approaches is important.

Making use of high-quality filler materials and protecting gases that are appropriate for the base steel and welding procedure can significantly decrease the danger of porosity. Furthermore, preserving correct welding specifications, such as voltage, existing, take a trip speed, and gas circulation rate, is vital for porosity prevention.
Moreover, employing correct welding methods, such as keeping a regular traveling speed, electrode angle, and arc size, can aid protect against he said porosity (What is Porosity). Appropriate training of welders to guarantee they follow ideal methods and quality assurance treatments is also important in decreasing porosity defects in welding

Best Practices for Quality Welds
Guaranteeing adherence to sector standards and proper weld joint preparation are fundamental elements of attaining continually top quality welds. In addition to these foundational actions, there are numerous best methods that welders can apply to even more boost the high quality of their company website welds. One trick technique is keeping appropriate cleanliness in the welding area. Contaminants such as oil, grease, rust, and paint can detrimentally influence the quality of the weld, resulting in problems. Extensively cleaning up the workpiece and surrounding location prior to welding can assist alleviate these concerns.
An additional finest practice is to thoroughly select the ideal welding specifications for the details products being joined. This consists of setting the correct voltage, existing, travel speed, and securing gas flow price. Appropriate parameter option makes sure optimal weld infiltration, fusion, and general high quality. Using top notch welding consumables, such as electrodes and filler metals, can dramatically impact the last weld quality. Purchasing premium consumables can lead to more powerful, much more sturdy welds with fewer issues. By following these ideal practices, welders can constantly produce premium welds that meet industry criteria and exceed client assumptions.
Importance of Porosity Control
Porosity control plays a vital duty in ensuring the stability and high quality of welding joints. Porosity, defined by the visibility of dental caries or gaps within the weld steel, can substantially jeopardize the mechanical residential or commercial properties and architectural stability of the weld. Extreme porosity compromises the weld, making it more susceptible to fracturing, deterioration, and general failure under functional lots.
Reliable porosity control is necessary for maintaining the desired mechanical properties, such as strength, ductility, and sturdiness, of the bonded joint. What is Porosity. By lessening porosity, welders can improve the overall quality and integrity of the weld, making certain that it satisfies the efficiency demands of the intended application
Furthermore, porosity control is vital for attaining the desired aesthetic appearance of the weld. Too much porosity not only weakens the weld yet likewise interferes with its aesthetic appeal, which can be crucial in sectors where aesthetics are important. Appropriate porosity control techniques, such as making use of the appropriate shielding gas, managing the welding parameters, and making certain appropriate sanitation of the base materials, are essential for creating top quality welds with marginal problems.
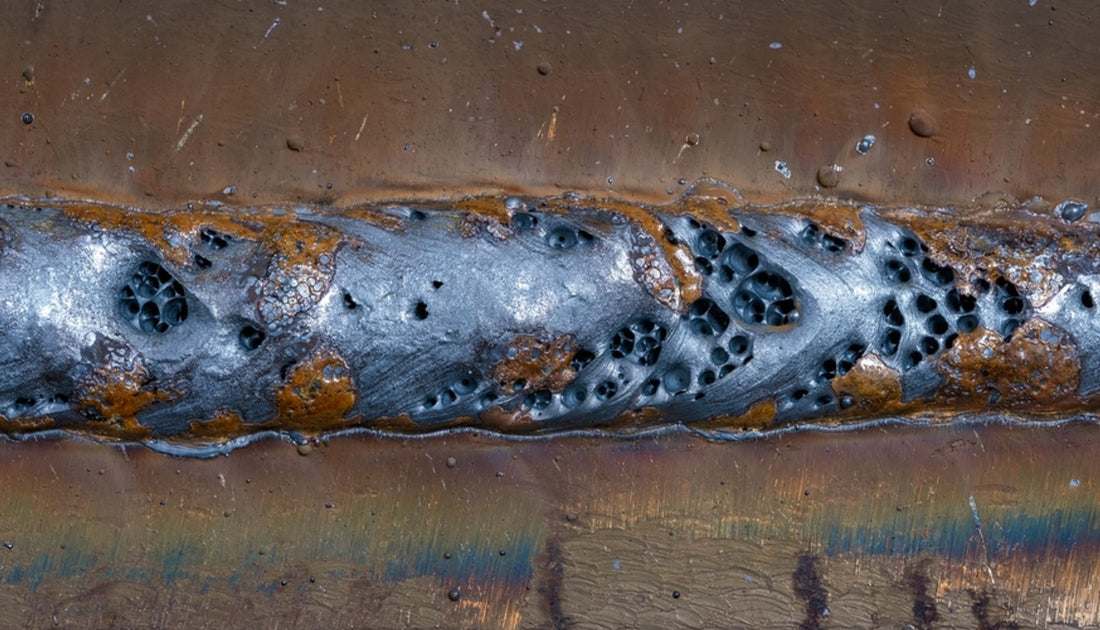
Verdict
Finally, porosity in welding is a typical defect that can jeopardize the top quality of the weld. By understanding the causes of porosity and applying proper avoidance methods, welders can decrease flaws and achieve better welds. It is necessary to control porosity in welding to resource make sure the integrity and toughness of the end product. Applying best techniques for porosity control is essential for attaining optimal welding outcomes.